加工対応事例Case study
投資金額を抑えて貼り合わせ効率を良くしたい
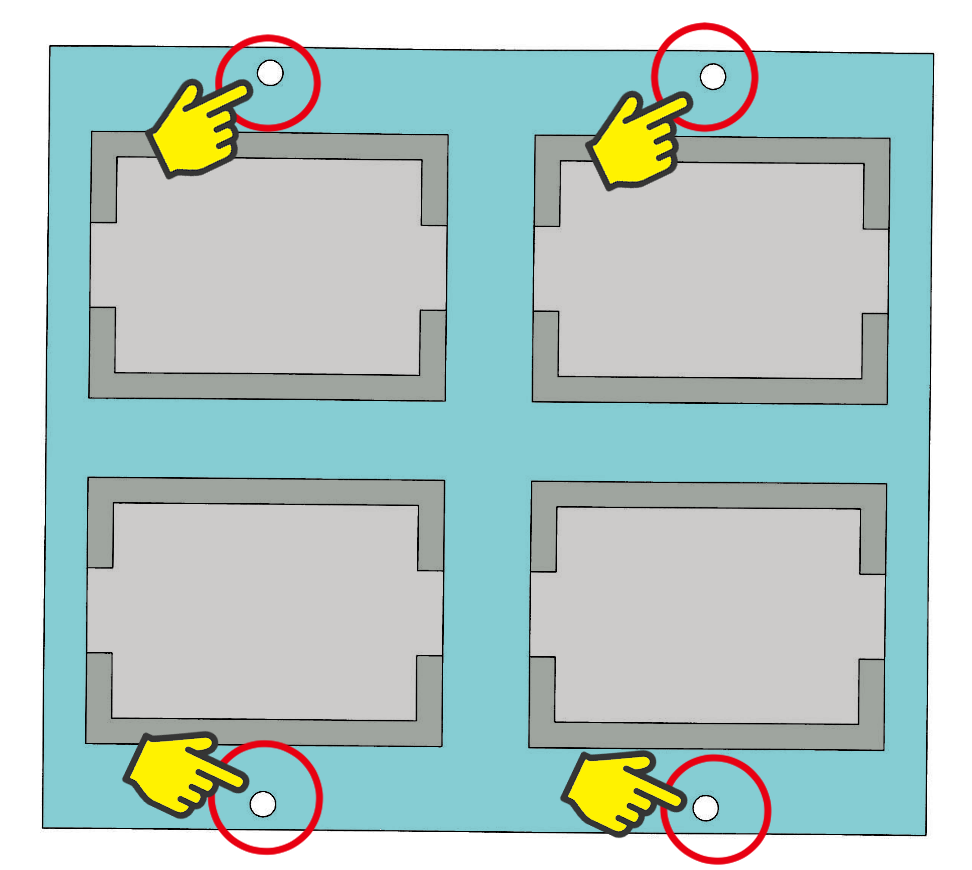
目的 | 貼り合わせ工程の生産タクトを向上させ、作業コストを低減 |
---|---|
機能 | 治具貼りによる半自動化 |
加工のキモ | 高精度な位置決め孔が付与されたシート加工品 |
お客さまが抱える課題
高騰する人件費、激化する価格競争
車載製品の表示パネル、液晶バックライトに使用される拡散シート加工品。
これまでは1枚ずつ手作業による貼り合わせ工程で生産されていたが、年々高騰する人件費に反して市場での価格競争は厳しくなる一方で生産コストの低減は避けて通れない課題となっていた。
自動化設備の初期投資がネックに
ユーザー様では生産コストの低減に向けて、技術チームによる貼り合わせ工程の自動化が検討されていたが、自動貼り合わせの設備は非常に高額な初期投資が必要になる。しかしながらこの設備は特定品番の貼り合わせ専用機でしかなく工場内での汎用性がなかった。そのため設備の償却費がネックとなり設備導入は容易でなく自動化の検討は難航していた。
課題解決のポイント
これ使えるんじゃない?
この拡散シートには、加工の際に使用するスプロケット孔がシート両端に開いているが、自動化検討の技術チームはこれに注目した。「これを貼り合わせ効率化に使えるんじゃないか?」
早速、このスプロケット孔の位置精度が貼り合わせの精度に見合ったものか?を検証したところ、じゅうぶんに使える精度であることが判明した。
高額な自動貼り設備を導入せずに・・・
このスプロケット孔を活用して複数個の製品をシート単位で貼り合わせる治具なら低コストで作ることができる。半自動にはなってしまうが高額投資をしなくてもかなりの効率化が実現できた。
効果的な改善につながった加工精度
今回の工程改善につながった位置決めのスプロケット孔は、もともとのシート加工に必要な孔だったため、金型の再作成などは必要なく、追加のイニシャルコストも発生しなかった。
高精度で加工されたシートの孔を、そのまま貼り合わせ工程の位置決め孔として使えたことが低予算で効果的な改善を実現させた。